1. Fiber Optic Sensors
(1). Fiber optic acoustic emission sensors
Acoustic Emission (AE) is a term used to describe the sound waves produced when a material undergoes stress (internal change) as a result of an external force. AE is a phenomenon that occurs, for instance, in mechanical loadings that generate sources of elastic waves. Acoustic emission technology, as a method of structural health monitoring, has been developed and applied. Our group focuses on:
(a) Novel fiber optic acoustic emission sensor based on fused-tapered fiber coupler has been invented.
(b) A fiber optic acoustic emission sensor based on a fused-tapered fiber coupler has been invented and embedded in composite materials for monitoring composite materials and structures damage. Linear damage location on an aluminum plate and a composite plate has been verified utilizing a pair of fused-tapered fiber couplers.

Fig. 1 Schematic illustration of Fiber optic acoustic emission sensor
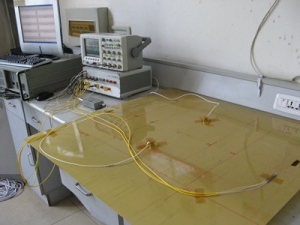
Fig. 2 Setup of acoustic emission technology with fiber optic sensors and PZT
(2). Fiber Bragg grating sensors
A fiber Bragg grating (FBG) is a type of distributed Bragg reflector constructed in a short segment of optical fiber that reflects particular wavelengths of light and transmits all others. This is achieved by creating a periodic variation in the refractive index of the fiber core which generates a wavelength-specific dielectric mirror. A fiber Bragg grating can, therefore, be used as an inline optical filter to block certain wavelengths or as a wavelength-specific reflector.
As well as being sensitive to strain, the Bragg wavelength is also sensitive to temperature. This means that fiber Bragg gratings can be used as sensing elements in optical fiber sensors. In a FBG sensor, the measurand causes a shift in the Bragg wavelength. The relative shift in the Bragg wavelength due to an applied strain is given by:
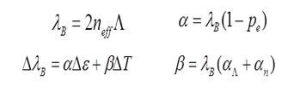
2. Structural Health Monitoring
A series of Fiber Optic Sensors (FOSs) and its measurement systems with multi-parameters have been developed and applied for Structural Health Monitoring (SHM) of composite materials and structures. These FOSs can measure strain, temperature, and acoustic emission. It can also be used for monitoring the processes of manufacturing composites. The measure systems based on TDM technology realize multi-channels measure for Fiber Bragg Grating (FBG). Various kinds of FOSs have been applied for the research of manufacturing composites and the residual strain regulation which propose a novel monitoring method for residual strain from the structure.
(a) The fiber optic acoustic emission sensor is applied for real-time monitoring of composite materials and structure's damage and identification. Research achievements supply important polytechnic design parameters of composite materials and structures and monitoring and control technology for applications in departments such as aviation, aerospace, etc.
(b) The Fiber Bragg Grating (FBG) sensor is applied for deformation monitoring of flexible variable camber wing and two-dimensional shape deformation of a shape memory polymer plate as a vector bending sensor.
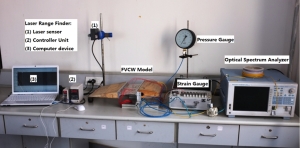
Fig. 3 A flexible variable camber wing model with four FBG sensors

Fig. 4 Smart wind turbine blade static load test set-up